- SUSTAINABUILT®
- Posts
- Serial refurbishment - modular construction for existing buildings
Serial refurbishment - modular construction for existing buildings
While newly constructed buildings meet high energy standards, the energy modernization of existing buildings is stagnating.
There are around 22 million buildings in Germany, which are responsible for around a third of greenhouse gas emissions. While newly constructed buildings meet high energy standards, the energy modernization of existing buildings is stagnating. The current building stock is outdated and no longer meets the requirements for accessibility, comfort and energy efficiency. Nevertheless, these buildings play an important role in climate targets, as most were built before 1977 without thermal insulation guidelines. (see dena_Gebaeudereport_2023.pdf viewed on 29.11.2023, at 22:31)
All buildings are to be modernized in a climate-neutral way by 2050, which poses major challenges for the construction industry.
In order to promote refurbishments, the “Serial Refurbishment” bonus was introduced as part of the Federal Funding for Efficient Buildings (BEG), which supports the use of prefabricated façade and roof elements. (see Serielles Sanieren – der neue Bonus | KfW viewed on 29.11.2023, at 22:45)
This method is intended to increase renovation rates and enables simpler and faster installation compared to conventional methods.
The use of prefabricated timber elements in new buildings is common practice and has also become established in the renovation sector. Serial refurbishment, particularly for simpler and similar buildings, offers cost-effective refurbishment solutions for around 2.3 million buildings, including many from the 1950s to 1970s. This is important as rents in these buildings cannot be allowed to rise for social reasons. There is potential to create around 1.1 million low-cost apartments by adding storeys.
Renovation with prefabricated timber elements makes it possible to add storeys to existing buildings and offers the potential to renovate between 3.8 and 6.5 million residential units, with a market volume of between 30 and 120 billion euros. (cf. Studie bestätigt Potenzial durch Aufstockung / 2,7 Millionen Wohnungen - Architektur und Architekten - News / Meldungen / Nachrichten - BauNetz.deviewed on 29.11.2023, at 23:45) The preservation of existing buildings holds ecological potential in contrast to demolition and disposal of building materials.
The modernization of existing buildings using prefabricated timber frame elements offers a high-quality and versatile method of aligning standards with new buildings. This method not only fulfills economic, building law and construction requirements such as thermal, fire and sound insulation as well as stability and earthquake safety, but also enables architectural improvements.
Thanks to the low weight of the timber elements, timber construction offers technical advantages. Computer-controlled production techniques enable even complex components to be produced in series.
The integration of prefabricated components offers opportunities to improve thermal comfort and fire safety and enables the integration of building services components. Such refurbishment methods can increase the number of residential units and can often be implemented during ongoing operations or with only brief interruptions to use.
The decision to use prefabricated façade elements should be made at an early stage of planning. The planning process is divided into three steps:
First, a digital survey is conducted to precisely capture the building's volume and exact shapes, which are then transferred into a 3D model. This data forms the basis for the subsequent planning steps. The overall planning then takes place from the preliminary design to the realization stage, involving all parties to ensure a smooth construction process. The Building Information Modeling (BIM) method is used here, where all relevant information is made accessible in the 3D model and can be edited by all planning participants. Interfaces and associated data are clearly defined in this process. In the final step, the specific planning for timber construction is carried out, where the 3D model is either directly transferred from the BIM planning into the timber construction software or created during the survey. This allows for precise adaptation of the facade elements to the building, fitting like a custom-made second skin. Based on the timber construction planning, the corresponding data for production is then generated.
The façade elements are secured with a compensating insulation layer to prevent thermal bridges. The installation of new windows and doors with triple glazing improves sound insulation.
The elements are installed from façade scaffolding or alternatively using work platforms. The high degree of prefabrication enables quick assembly and reduces construction time, which is particularly advantageous in urban areas and protects the building from the weather during construction. (see IDH-Serielles-Sanieren-2023-06_print150dpi_230912.pdf (informationsdienst-holz.de viewed on 30.11.2032, at 00:13)
Want to work with us?
Let's discover potential and opportunities together in a non-binding initial meeting. During this appointment, we will take time exclusively for your concerns.
We will discuss your goals and the challenges you face in your day-to-day project business and determine together how we can support you.
Contact us for a personalized consultation and learn more about the benefits for your next project.
Arrange a free initial consultation now.
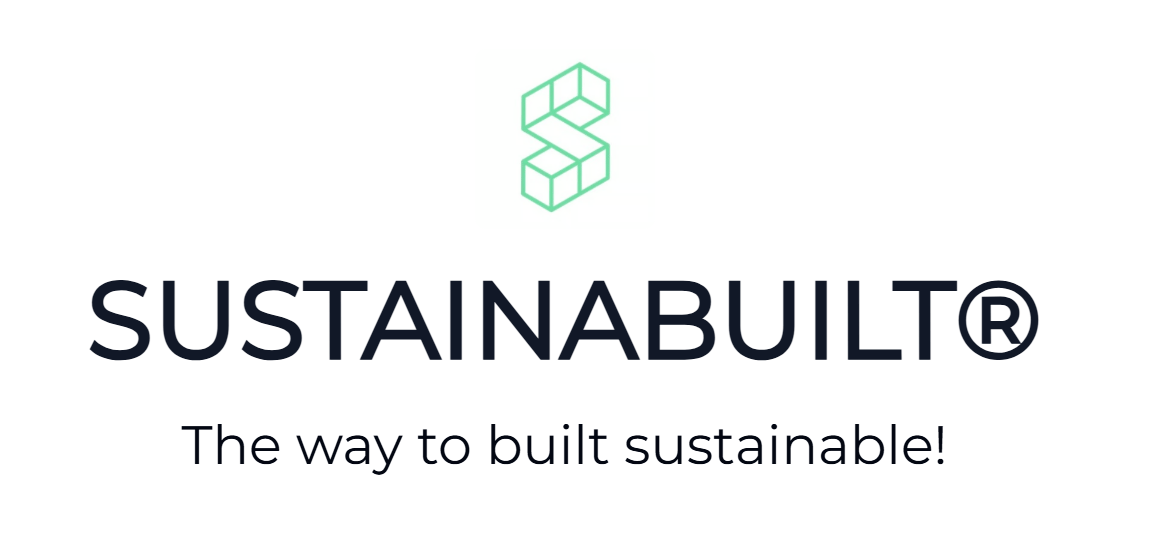