- SUSTAINABUILT®
- Posts
- Serial & modular construction - increasing efficiency through the use of robotics?
Serial & modular construction - increasing efficiency through the use of robotics?
Robotics in Timberconstruction
The use of robotics is becoming increasingly important in the construction industry worldwide. Nevertheless, the degree of automation in building construction is still low in most newly completed buildings.
This is primarily because serial construction has yet to gain a significant market share, there is skepticism regarding the use of robotics, and the digitization of planning is often still insufficiently advanced.
The product range includes a wide selection, from 3D concrete printers to highly automated robotic systems that are already in use today.
But which product is suitable for series production?
This edition focuses on the use of robotics in timber construction, as wood is currently considered the most environmentally friendly building material for serial new construction.
While prefabricated or already processed elements are often purchased from well-known manufacturers when using CLT/cross-laminated timber, the value-added depth in timber frame construction lies with the manufacturer itself. Therefore, manufacturers who primarily use prefabricated CLT/cross-laminated timber elements require smaller production sites and no robotic systems of their own. This results in highly compact production facilities that may be set up only temporarily for a larger construction project.
The use of robotics ensures consistent quality while reducing production costs. Moreover, in times of skilled labor shortages, robotics allows for continuous production. Robotics also makes production scheduling much more predictable.
Fundamentally, robotics can solve several major problems of current manufacturing technology:
Labor Shortages: For a large company, for example, the use of robotics could mean that in the future, only 12 employees will be needed in element construction instead of the current 62. For a family business, it could mean that only one employee is needed in element production (e.g., with the RANDEK ZeroLabor system: 1 person – 1 wall – 1 hour). One employee can produce elements in the factory, two-sided paneled and insulated with robotics, while other employees erect the building on-site or assemble 2-D elements into modules.
The space required for high volumes is smaller with intelligent use of robotics than with traditional manufacturing technology using multifunctional bridges. Intelligent means that multiple robots can work simultaneously in a cell in a process-safe and productivity-optimized manner. The tasks that need to be performed in the cell are clearly defined. Which robot takes on which task is determined fully automatically based on an AI-like process, for example, in the RANDEK ZeroLabor system. This ensures, at least when working with an experienced provider of robotics for timber frame construction, that the robots work together highly productively and process-safely in a confined space.
Human errors in manufacturing can be avoided since the robots do exactly what was drawn in the CAD during work preparation. No worker in the production process needs to look at a plan.
The quality remains consistently high. Even after many years in multi-shift operation, there are no deviations from the elements produced at the beginning.
The availability is significantly higher than with other systems (e.g., KUKA Quantec / ZeroLabor: 99.9% technical availability, average downtime-free operation: 400,000 operating hours*).
*Source: KUKA website
If something does happen, the average repair time can be significantly shorter than with other systems (e.g., KUKA Quantec / ZeroLabor: 0.25 operating hours*).
*Source: KUKA website
Intelligently used robotics is highly flexible. Various tools can be automatically exchanged, making it easy to cut and fasten different materials. Industrial, highly productive manufacturing and batch size 1 are therefore not a contradiction.
Robotics makes sense for both family and industrial businesses. One system is smaller, slower, and cheaper, while the other is larger and faster. The functionalities can be exactly the same.
*Source: Wolfgang Horn - HORN Hausbau Technologie, example RANDEK ZeroLabor
Standard CAD programs for timber frame construction can be used; if the system provider has done their homework, nothing changes in work preparation.
Aspects to Consider to Leverage the Benefits of Robotics (Which Few People Think About):
Timber construction differs fundamentally from other fields of robotics: the volumes are usually small (cf. automotive industry: robots alone install around 30,000 windshields per year on the Porsche 911, always the same process), the outlet in the living room is always in a different place (and if it's just 1 cm to the left, it has to be 1 cm to the left), the environment can be dusty, and the material wood has greater tolerances than plastic or metal. Therefore, experiences from other industries cannot be transferred to timber construction practice, and several attempts by relevant providers have failed so far. A successful provider of robotics for timber frame construction should therefore have many years of experience in timber frame construction and long, intensive practical experience in robotics.
The benefits of robotics can only be leveraged if robotics is used intelligently (keywords: flexibility/batch size 1; space requirements for large volumes, teamwork of robots). This intelligent programming is complex and one of the cost drivers for systems with intelligent robotics. A provider should have a correspondingly large and competent team of robotics specialists dedicated to timber frame construction.
The control of robotics is different, for example, from multifunctional bridges. This means that the programs that automatically translate the CAD drawing from work preparation for the robots cannot be the same as those for CNC-controlled multifunctional bridges. Some providers of traditional machinery technology, therefore, struggle more with robotics than one would expect. Providers who are just now entering robotics for timber frame construction may not be able to deliver mature translation programs with their first systems, as feedback from daily practice is completely lacking. With providers who have had numerous robotic cells for timber frame construction in practical use for several years, customers can assume that the translation works flawlessly and the robots automatically, flexibly, and highly productively do exactly what was drawn in the standard CAD.
With traditional technology, more employees are needed, but manual intervention is still possible without significantly increasing processing time. If a plate cutout falls into the table of the multifunctional bridge, the employee can simply remove it. The employee and the time for manual removal of the cutouts are already factored into the production time. In a fully automatic system where all processes are carried out by robots and manual intervention in the cell is not intended, process safety is a knockout criterion. If a process does not work, the entire system stops. Neither employees nor time for manual interventions are factored in.
Fundamentally, robots can do almost anything. However, to achieve the desired productivity, it is often crucial how a wall element is designed. Two walls that look exactly the same from the outside with all windows, outlets, etc., and have the same insulation values, can be constructed differently. The production time of the two walls can therefore vary greatly, even though the technical data and appearance are the same. Experienced system engineers, therefore, advise module or prefab house builders on the topic of manufacturing-optimized design (DFM = Design for Manufacturing). For a "1 person – 1 wall – 1 hour" system for a family business, this does not play a significant role. For a high-performance system for large volumes, DFM can make the difference. Robotics for timber frame construction without DFM is a bit like racing Formula 1 without the race engineer who gives the driver instructions on where to gain the crucial seconds. Even the best Formula 1 car will lose the race.
Robots are inherently highly flexible. A base system that is always the same (=standardized) for all systems but can be expanded and supplemented as needed makes great sense. Standardized system technology (part uniformity, identical software, easily upgradeable new apps) means process safety. A modular, standardized system will usually always be more process-safe than a custom-developed system. Process safety is a knockout criterion when using robotics.
Put very pointedly, robots are nowadays tools like screwdrivers used to be. What matters is not the robot (or screwdriver) but the competence, creativity, and, above all, the practical experience of the robotics integrator* (or the user with the screwdriver) in timber frame construction. This competence and experience are ultimately decisive for the success of a system with robotics. Company that equips and programs robots for specific applications
While all important data are known in traditional machinery technology, only the system builder/robotics integrator can provide information on how large a system needs to be with a corresponding volume, where elements should possibly be discharged, how the plumbing installation is best carried out, or where buffer tables are needed in fully automatic systems with robotics. Therefore, system planning should involve discussions with the system builder/robotics integrator from the start. It is not uncommon to initially consult several providers and discuss the various possibilities and different system technologies.
Conclusion
Production workers supported by modern CNC machines are well "calculable" and have proven themselves in practice.
Nevertheless, the application of robotics in timber construction can increase a manufacturer's production efficiency.
However, this requires the highest trust in the technology of the system provider, their competence in both timber frame construction and robotics, know-how in setting up and commissioning the IT infrastructure (specialized software/robotics engineers and flawlessly functioning post-processors), and years of experience of the supplier with corresponding systems in real-world operations.
Robotics enables batch size 1! The problem is not robotics. The problem is system providers who have not done their homework—mainly concerning control technology and software—and therefore offer inflexible systems for always the same wall elements. If the system provider has the corresponding practical experience and competence, they can offer systems that produce batch size 1 faster than an inexperienced provider takes to produce a standardized wall element!
There are only a few system providers who already have sufficient practical experience with the application of robotics in timber construction, and thus, incorrect decisions can lead to unforeseeable, incalculable risks that deter from making a fundamental decision.
In my opinion, for timber construction to make a significant contribution to the government's new construction goals, the use of robotics is indispensable.
Example videos from Randek “Zero Labor”
Want to work with us?
Let's discover potential and opportunities together in a non-binding initial meeting. During this appointment, we will take time exclusively for your concerns.
We will discuss your goals and the challenges you face in your day-to-day project business and determine together how we can support you.
Contact us for a personalized consultation and learn more about the benefits for your next project.
Arrange a free initial consultation now.
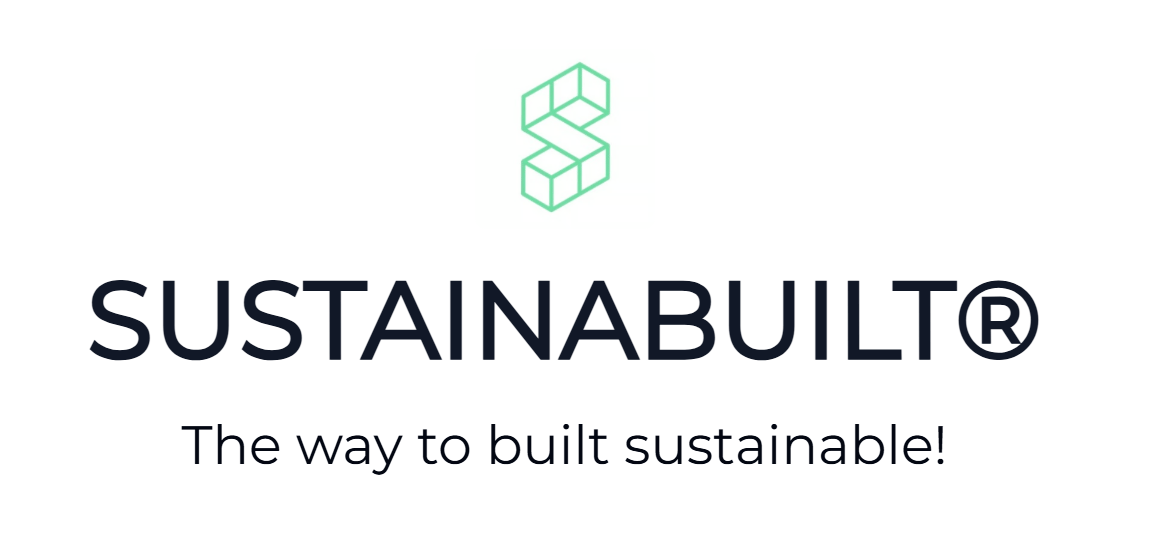